Glass for curtain walls: types, thickness and key considerations
Share this blog:
Glass is a common material for curtain wall infills. But not any old glass will do. Learn more in our article.

जब पहले कांच-उड़ाने वालों ने कांच से जार और फूलदान बनाए, तो उन्होंने कभी यह विश्वास नहीं किया होगा कि एक दिन पूरी इमारतें कांच से बनाई जाएंगी।
फिर भी हम 21वीं सदी में ऐसे वित्तीय जिलों में रह रहे हैं, जहाँ गिलास बनाने वाली फैक्ट्री से भी ज़्यादा कांच का इस्तेमाल होता है। गगनचुंबी इमारतें, पुल, लिफ्ट, सीढ़ियाँ - किसी भी वास्तुशिल्प विशेषता का नाम लें और दुनिया में कहीं न कहीं शायद कांच का एक संस्करण ज़रूर होगा।
संरचनात्मक ग्लेज़िंग के अधिकांश उदाहरणों में, भार वहन करने की क्षमता सर्वोपरि है। यह मानव भार (कांच के रास्ते पर चलने वाले लोग) या संरचनात्मक भार (कांच की दीवार के ऊपर छत) हो सकता है। किसी भी मामले में, सुरक्षा को अधिकतम करने के लिए भार वहन करने की क्षमता सख्त नियमों द्वारा नियंत्रित होती है।
इसके विपरीत, पर्दे वाली दीवारें कोई संरचनात्मक भार नहीं उठाती हैं। वास्तव में, वे गैर-संरचनात्मक हैं। उनका काम इमारत के किसी अन्य हिस्से को सहारा देना नहीं है। इसके बजाय, वे इमारत को ढकती हैं, उसे मौसम से बचाती हैं।
This means it can be made from lightweight materials. But there's lightweight and then there's
lightweight. The job of a curtain wall is to shield a building from wind, rain, debris and even hurricanes. Rice paper isn't going to cut it.
दूसरी ओर, कांच ऐसा करेगा। कांच "इनफिल्स" के लिए सामग्री का सिर्फ़ एक विकल्प है, जैसा कि वे जाने जाते हैं। लेकिन कई वास्तुकारों के लिए, यह कोई मुश्किल काम नहीं है।
पर्दे की दीवार के लिए ग्लास सही प्रकार और मोटाई का होना चाहिए - और कुछ ऐसे विचार हैं जो सभी संरचनात्मक ग्लेज़िंग पर लागू नहीं होते हैं। इस लेख में, हम आपको उनके बारे में बताते हैं।
पर्दा दीवार प्रणाली क्या है?
पर्दे की दीवारें और पर्दे की दीवार प्रणाली नाम के अलावा सभी मामलों में एक जैसी हैं। एक प्रणाली में एक फ्रेम शामिल होगा, जो आम तौर पर एल्यूमीनियम से बना होता है, और इनफिल्स। ये कांच, पत्थर के लिबास, धातु के पैनल या लौवर से बने हो सकते हैं।
कर्टेन वॉल सिस्टम कई मंजिलों को कवर करते हैं। यह उन्हें स्टोरफ्रंट सिस्टम से अलग करता है, जो आम तौर पर सिर्फ़ एक मंजिल को कवर करते हैं। उन्हें वास्तुकला में आधुनिकतावादी आंदोलन के साथ पहचाना जाता है।
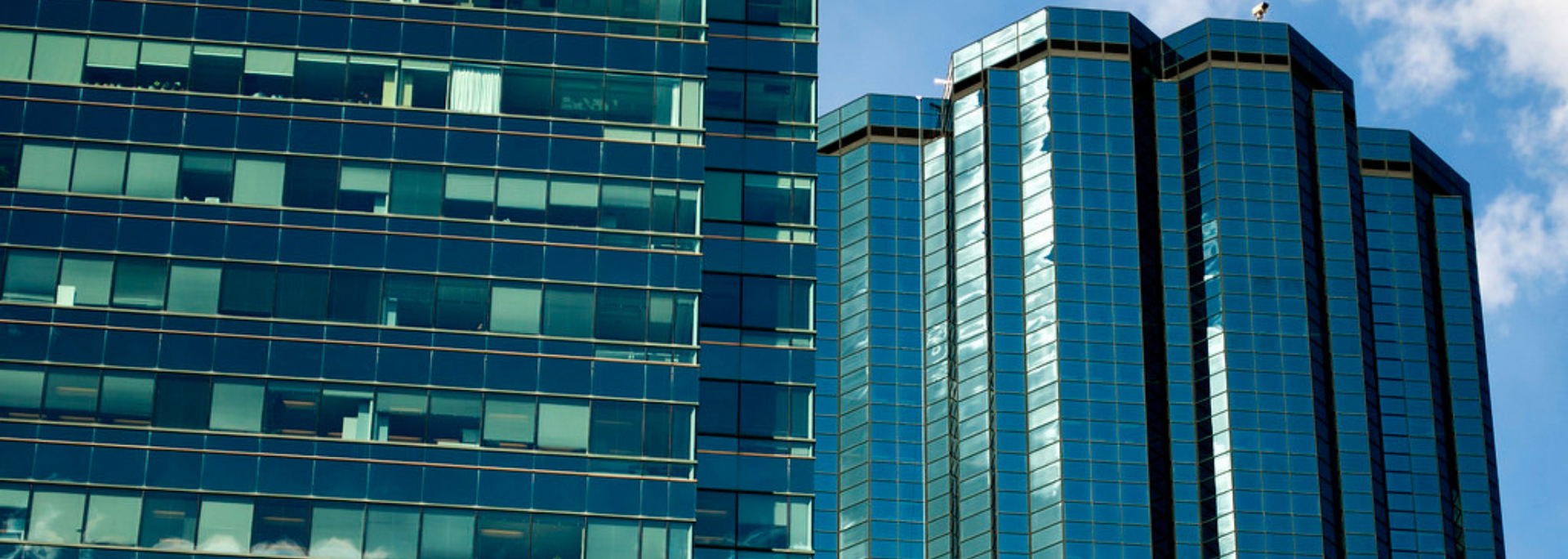
पर्दे की दीवार के लिए कांच का चयन क्यों करें?
इनफिल्स को कई तरह की सामग्रियों से बनाया जा सकता है। लेकिन हमारे पैसे के हिसाब से, कांच तीन मुख्य कारणों से सबसे अच्छा है।
सबसे पहले, यह एक किफायती सामग्री है। कांच के साथ काम करने से परियोजना की कुल लागत कम हो सकती है - ऐसा कुछ जिसका सभी द्वारा स्वागत किया जाएगा, खासकर जब कीमत में कमी से गुणवत्ता या सुरक्षा में कोई कमी नहीं आती है।
दूसरा, इसे व्यापक रूप से सौंदर्य की दृष्टि से आकर्षक माना जाता है। कांच की पर्दे वाली दीवारें कई शहरों में एक कारण से एक परिचित दृश्य हैं। आर्किटेक्ट उन्हें उनके चिकने, न्यूनतम, अव्यवस्थित रूप के लिए रेट करते हैं।
Taste is subjective, of course. But whatever your personal opinion, it's undeniable that
architectural glass looks grand, imposing and modern, whether you're at the airport or walking through the financial district.
अंतिम लेकिन महत्वपूर्ण बात यह है कि कांच की दीवारें प्राकृतिक प्रकाश को इमारत में आने देती हैं। यह व्यवसाय के कार्बन पदचिह्न के लिए अच्छा है, जिससे कृत्रिम प्रकाश की आवश्यकता नाटकीय रूप से कम हो जाती है।
ऐसा कहा जाता है कि इससे कर्मचारियों का मनोबल भी बढ़ता है। सिर्फ़ रोशनी से आप खुश नहीं हो सकते - लेकिन सूरज की रोशनी से भरे एक बड़े दफ़्तर और एक तंग खिड़की रहित सेल के बीच का अंतर साफ़ है।
इन सभी कारणों से, कांच का इस्तेमाल पर्दे की दीवार के लिए पसंदीदा सामग्री के रूप में व्यापक रूप से किया जाता है। लेकिन कोई भी पुराना कांच काम नहीं करेगा।
पर्दे की दीवारों के लिए कांच के प्रकार
पर्दे की दीवारों के लिए सबसे आम सामग्री फ्लोट ग्लास है। इस प्रकार के ग्लास का आविष्कार 1900 के दशक में पिल्किंगटन ने किया था और तब से यह एक मुख्य सामग्री रही है।
फ्लोट ग्लास की प्रसिद्धि का एक कारण इसकी बहुमुखी प्रतिभा है। ग्राहक और आर्किटेक्ट कई तरह के रंगों और अपारदर्शिताओं में से चुन सकते हैं। इसे मिलीमीटर तक के आकार में काटा भी जा सकता है।
पर्दे की दीवार का कांच आमतौर पर पारदर्शी होता है, लेकिन कभी-कभी अतिरिक्त गोपनीयता या विशिष्ट सौंदर्य प्रभावों के लिए पारभासी कांच का उपयोग किया जाता है। अपारदर्शी कांच का उपयोग कभी-कभी पर्दे की दीवार के पीछे की विशेषताओं को छिपाने के लिए भी किया जाता है।
स्थानीय भवन विनियमों और विशिष्ट परियोजना आवश्यकताओं के आधार पर, कांच को कठोर या लेमिनेट भी किया जा सकता है।
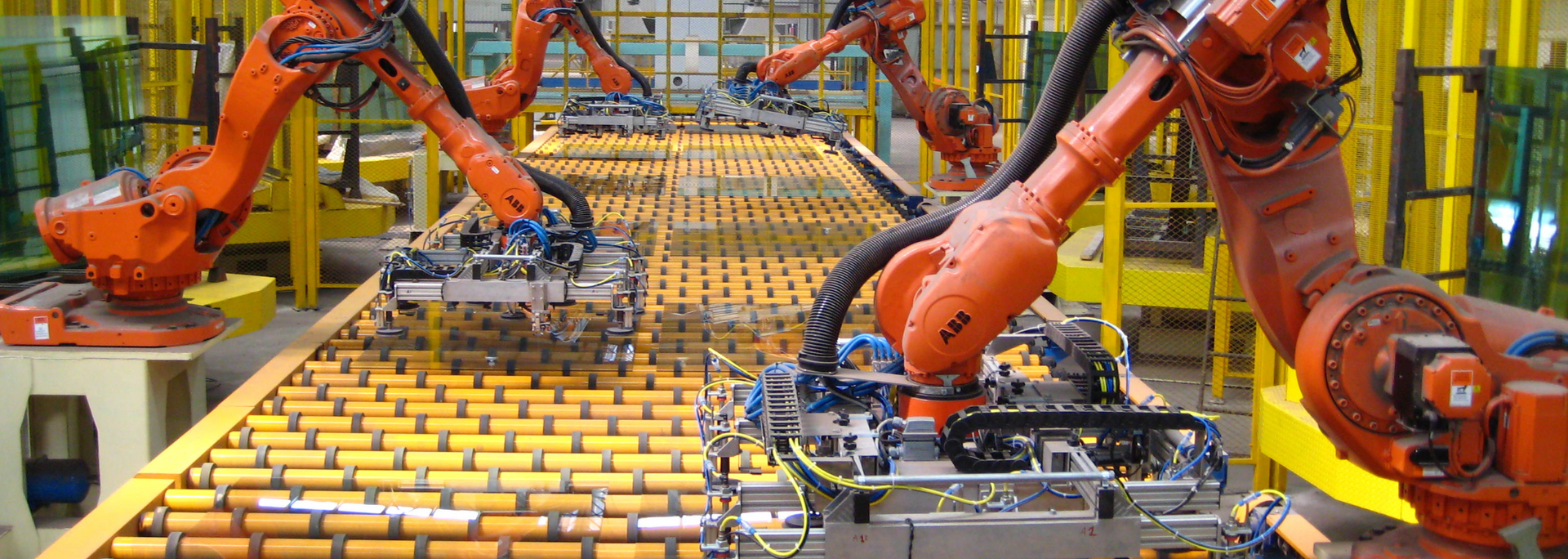
आग लगने की स्थिति में कई पर्दे की दीवारों में नॉक-आउट पैनल होते हैं। फ्लोट ग्लास पैनल खतरनाक टुकड़ों में टूट सकता है जो गिरकर राहगीर को घायल कर सकते हैं। इसके विपरीत, कठोर ग्लास कई छोटे, हानिरहित टुकड़ों में टूट जाता है।
इस बीच, पर्दे की दीवारों को विस्फोट-रोधी बनाने के लिए लेमिनेटेड ग्लास का उपयोग किया जाता है। ओक्लाहोमा सिटी, ओक्लाहोमा में अल्फ्रेड पी मुर्राह फेडरल बिल्डिंग में बम विस्फोट के बाद से पर्दे की दीवार निर्माताओं, इंस्टॉलरों और डिजाइनरों के लिए यह प्राथमिकता रही है।
इस घातक ट्रक बम विस्फोट ने यह स्पष्ट कर दिया कि पर्दे की दीवारें विस्फोटों के प्रति संवेदनशील होती हैं। लेमिनेटेड ग्लास इस समस्या से निपटने में सक्षम है, क्योंकि यह टूटता नहीं है, बल्कि बिखरता है।
इसी तरह, तूफान से प्रभावित क्षेत्रों में पर्दे की दीवार प्रणालियों के लिए लेमिनेटेड ग्लास का उपयोग किया जाता है। इससे हवा से उड़ने वाले मलबे के पर्दे की दीवार से टकराने पर होने वाले नुकसान को सीमित किया जा सकता है।
पर्दे की दीवारें कितनी मोटी होनी चाहिए?
कांच उद्योग में, मोटाई एक महत्वपूर्ण विचार है। यह ऐसी चीज नहीं है जिसका अनुमान लगाया जा सके या जिसे अनदेखा किया जा सके। यह कहना कोई अतिशयोक्ति नहीं है कि संरचनात्मक ग्लेज़िंग में, एक मिलीमीटर जीवन और मृत्यु के बीच का अंतर हो सकता है।
वाणिज्यिक और घरेलू दोनों तरह की कर्टेन वॉल प्रणालियों में, दो तरह की कांच की मोटाई पर विचार करना होता है। पहला मोनोलिथिक ग्लास के लिए है, जिसका इस्तेमाल आमतौर पर स्पैन्ड्रेल के लिए किया जाता है। दूसरा इन्सुलेटिंग ग्लास के लिए है, जो इमारत के बाकी हिस्सों को भरता है।
वाणिज्यिक परियोजनाओं में, मोनोलिथिक ग्लास आमतौर पर ¼ इंच या 6.4 मिलीमीटर होता है। इंसुलेटिंग ग्लास आमतौर पर एक इंच या 25 मिलीमीटर होता है। आवासीय परियोजनाओं में, मोनोलिथिक ग्लास आमतौर पर ⅛ इंच या 3.2 मिलीमीटर और इंसुलेटिंग ग्लास ⅝ इंच या 16 मिलीमीटर होता है।
हालांकि, ऐसी इमारतों में कांच मोटा हो सकता है, जहां अतिरिक्त ध्वनिरोधी या थर्मल नियंत्रण की आवश्यकता होती है - उदाहरण के लिए, रिकॉर्डिंग स्टूडियो में ध्वनिक ग्लास या प्रयोगशालाओं में सुरक्षात्मक ग्लास। कुछ मामलों में, पर्दे की दीवार का ग्लास ट्रिपल या यहां तक कि चौगुना-ग्लेज़्ड भी हो सकता है।
Looking for high-quality
glass for architecture? Look no further. Founded in 1993, ToughGlaze has become one of the UK's most trusted glass processing firms.
Get in touch today for a quick, competitive quote.